Abstract:
A tray to hold 12 ISCO bottles was previously designed without considering the weight of water when they are filled. The plastic tray was redesigned using Fusion360’s sheet material modeling and static stress simulation tools.
Introduction:
I was recently made aware that the design of the ISCO bottle trays did not consider the weight of the filled bottles (thank you, Azad, for noticing that)! Stresses in bent sheet materials are quite difficult to calculate by hand, so the design process for the new tray, under load, is as follows:
1. Initial Design
2. Perform Computer Simulation
3. Check results for low safety factor and high stress points
4. Redo Steps 1-3 until I am confident in the design
Design:
Let’s go over the initial design:
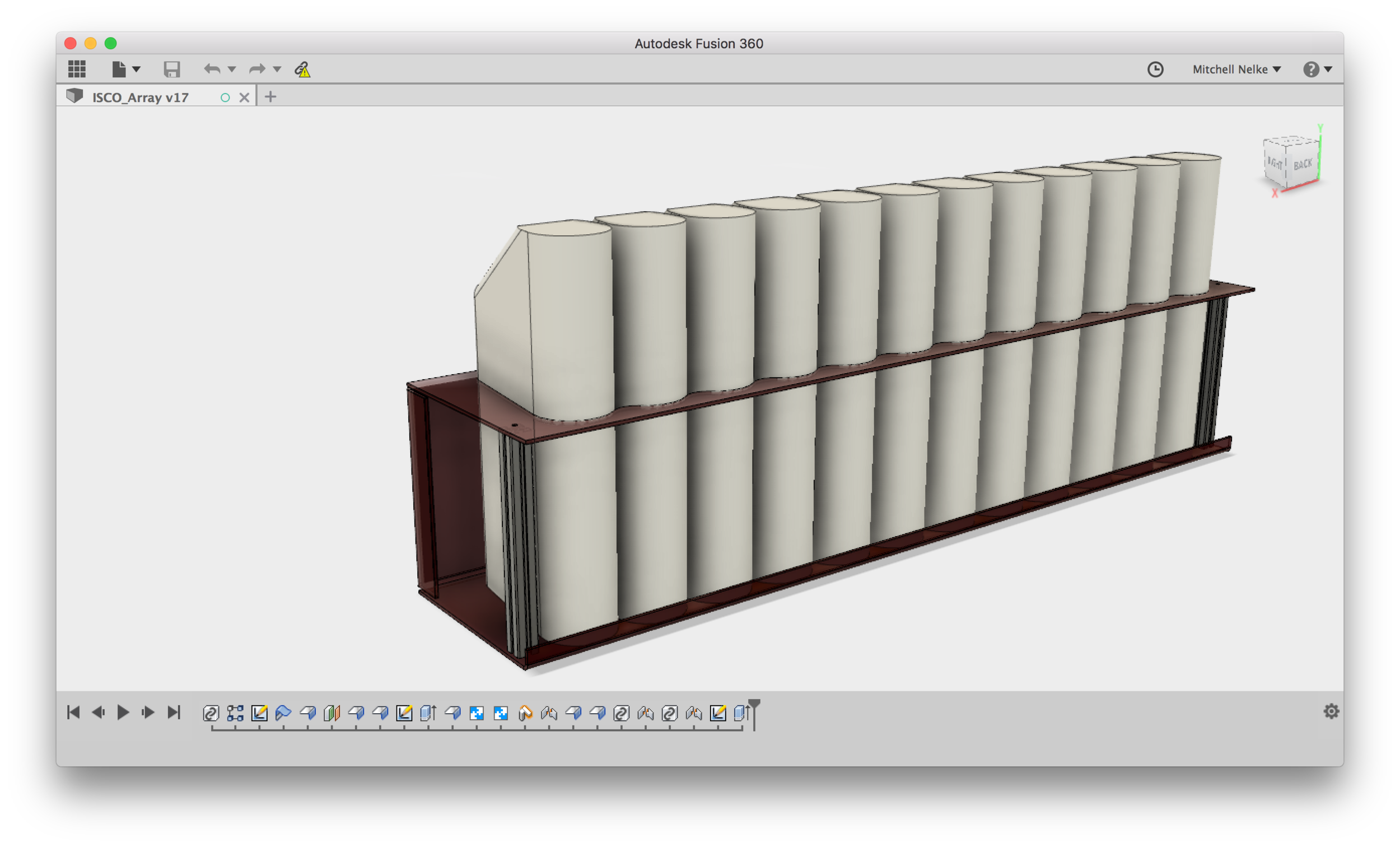
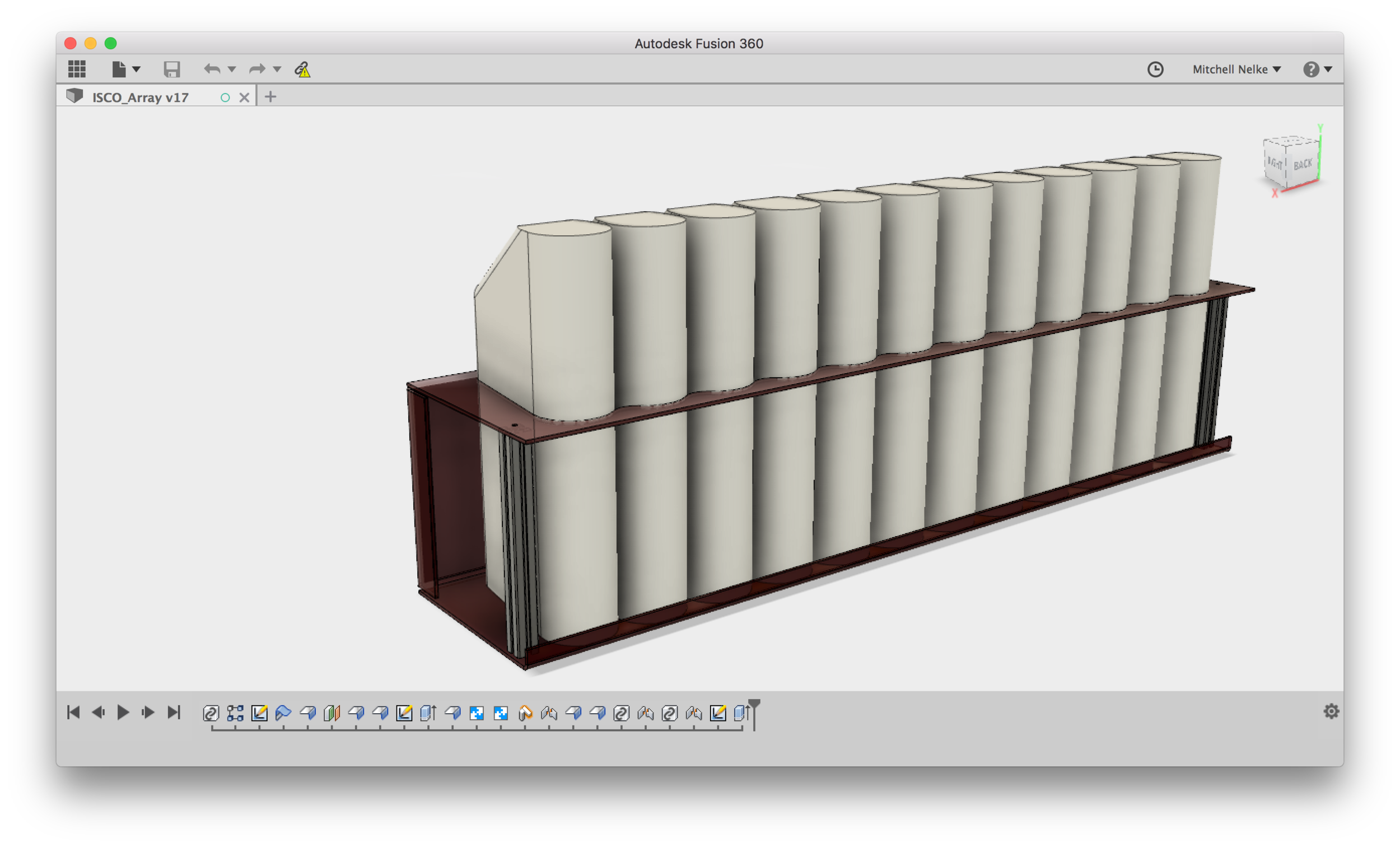
The ISCO bottles are split into two trays of 12. The constraints are as follows:
– No longer than 740mm long
– No wider than 160mm
– Flat Pattern cannot exceed 2” x 4” dimensions of stock sheet plastic
– Must hold 12kg (about evenly distributed along bottom face)
– Material is .04” (~1mm) PETG
The problem is the open face of the tray. By holding the shape of the tray by two pieces of aluminum extrusion, nearly all the weight of the bottles stresses two sets of M3 screws. Even with washers, the plastic would likely stretch or tear. The design was modified to address these issues.
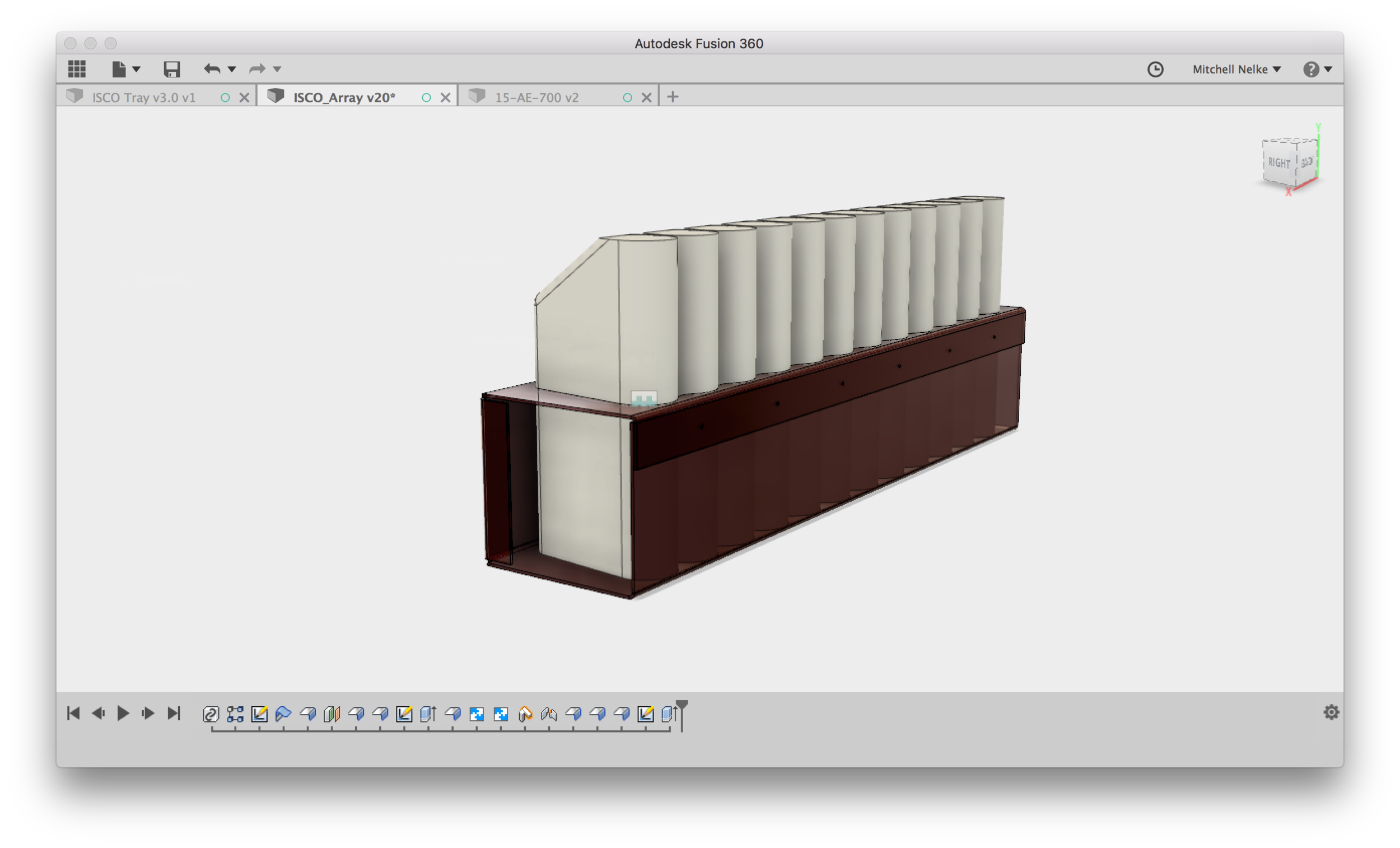
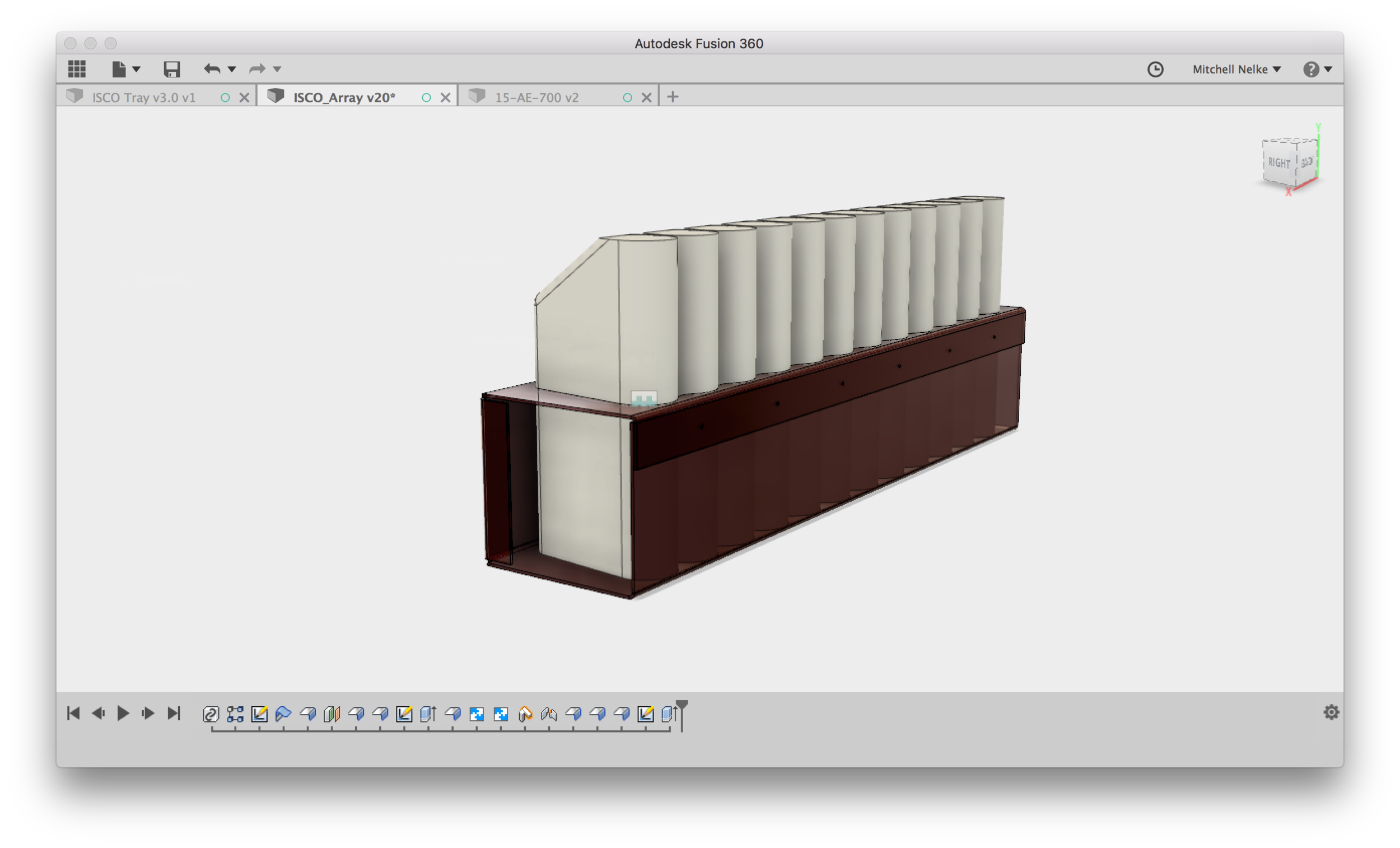
The new design uses a PETG sheet folded into an open-ended rectangular prism with an overlapping face. This overlapping face includes 6 holes for M3 machine screws and will also be glued together. Two kevlar straps for holding the device, connected on the bottom of the tray and tied with room at the top, are not shown. They will be located 1/3 of the length from either end.
The straps and glue are especially important because they aren’t included in the simulation. Because of them, I can assume that the safety factor for stresses on the sides and top of the tray can be lower than would be otherwise acceptable, since the straps will pull the device from the bottom face.
Simulation:
I performed a Static Stress simulation with a 120N distributed weight along the bottom face. The top face was constrained as “fixed”, and 6 ~M3 bolted connections were added on their respective holes, simulated as pinned connections, to hold the overlapping sides together.
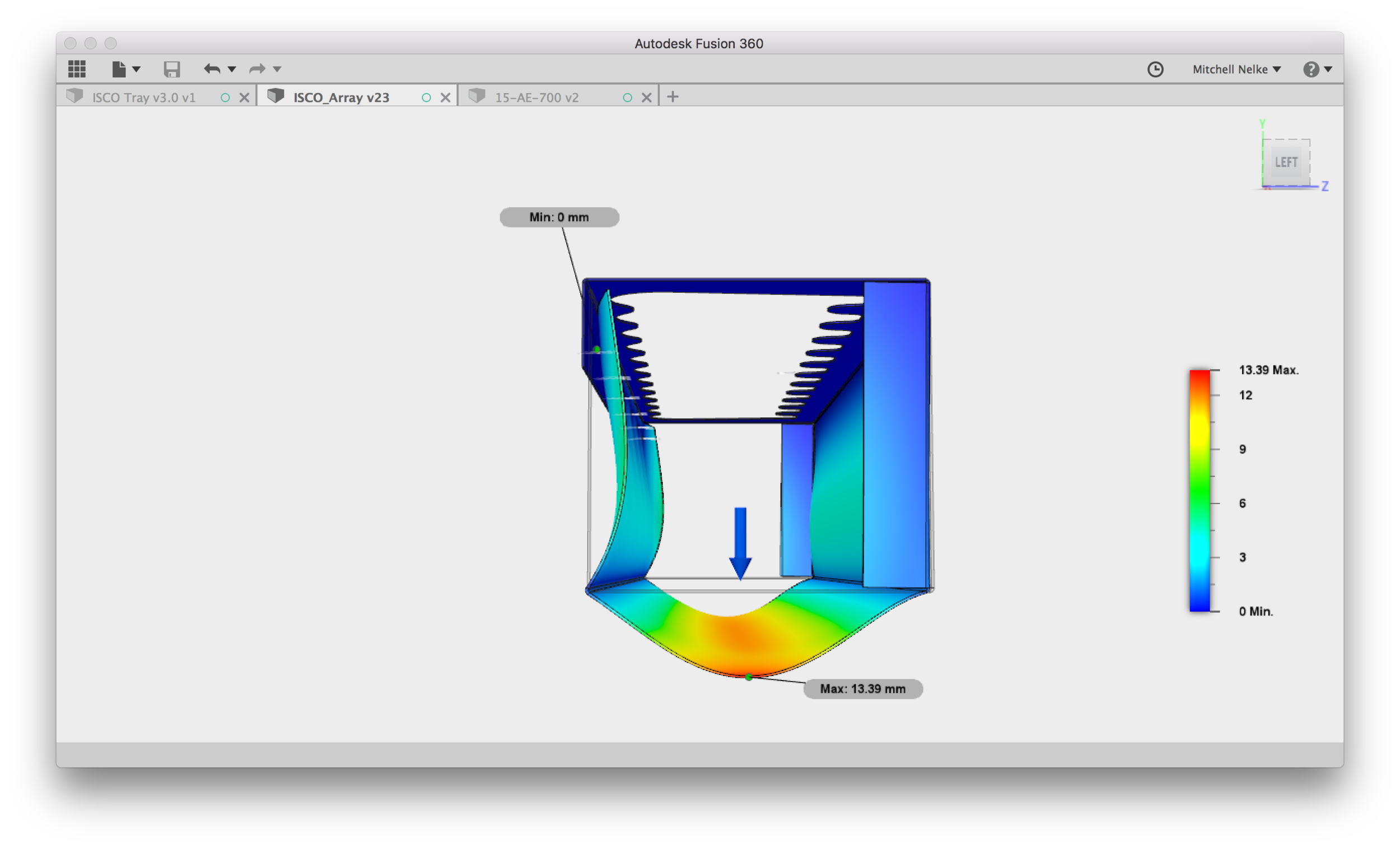
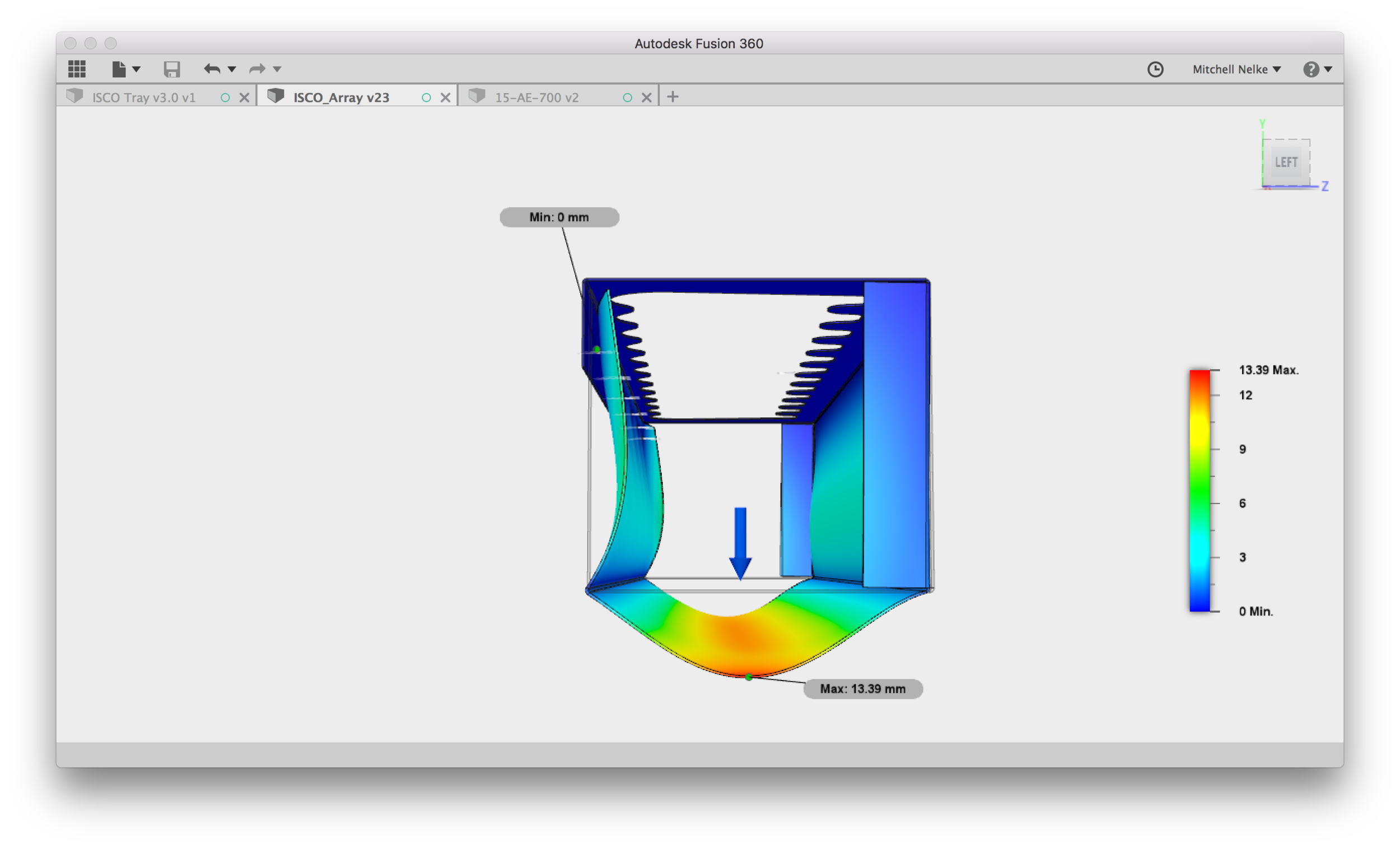
While the result of the simulation appears catastrophic in the above picture, it is important to know that Fusion360 greatly exaggerates displacement by default! The actual displacement should be about 13mm which will look much better. The addition of kevlar straps will likely have a negligible effect on this bottom displacement. Notice in the image below that the max stress is located at the bottom corner of the tray. Because the Yield Strength for PETG plastic is about 47MPa, a stress of 64MPa as shown would lead to stretching and possibly tearing along the edge. However, distributing the weight via kevlar straps along the bottom will minimize the stress along the edges of the tray, greatly improving the safety factor shown in the subsequent image.
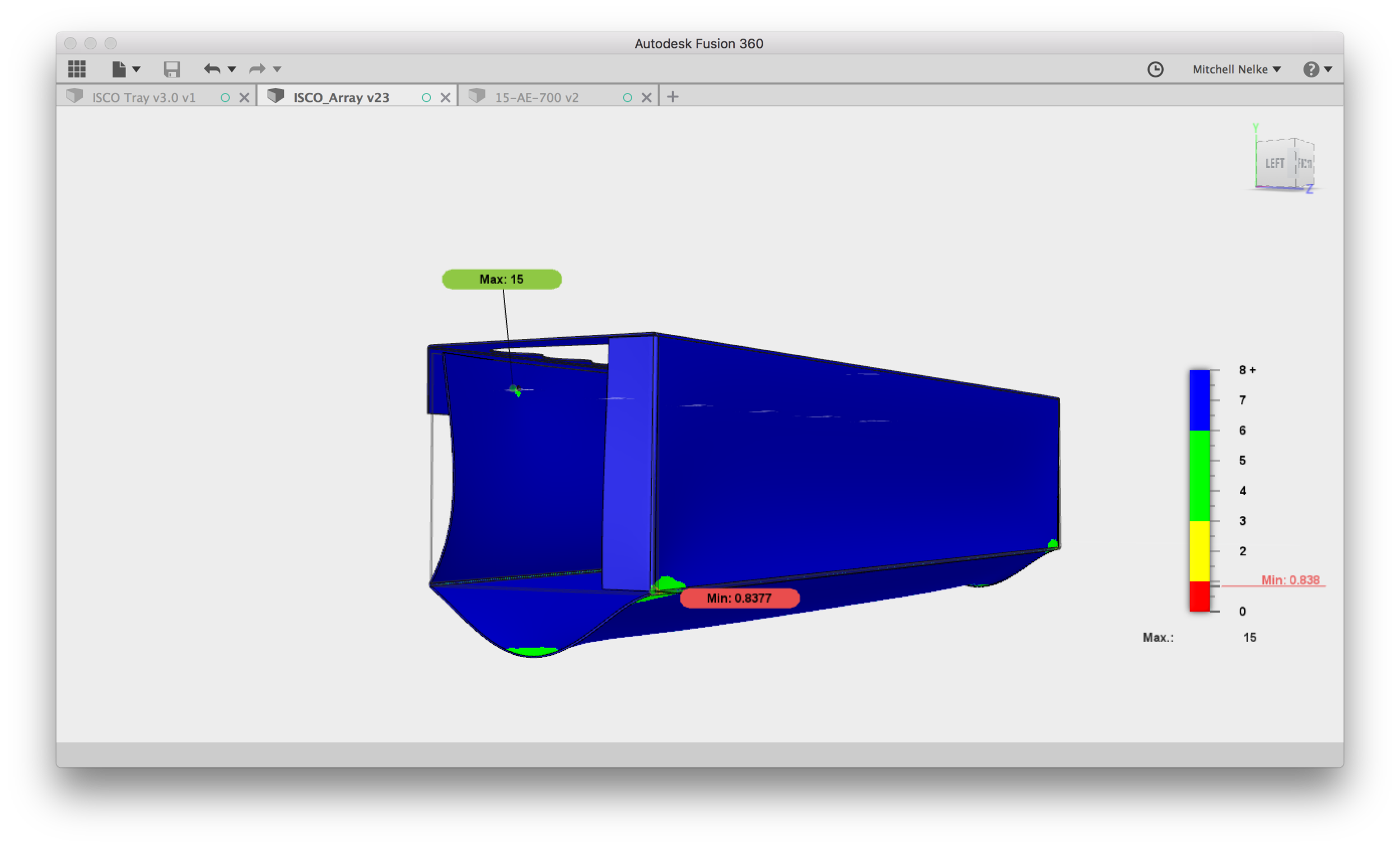
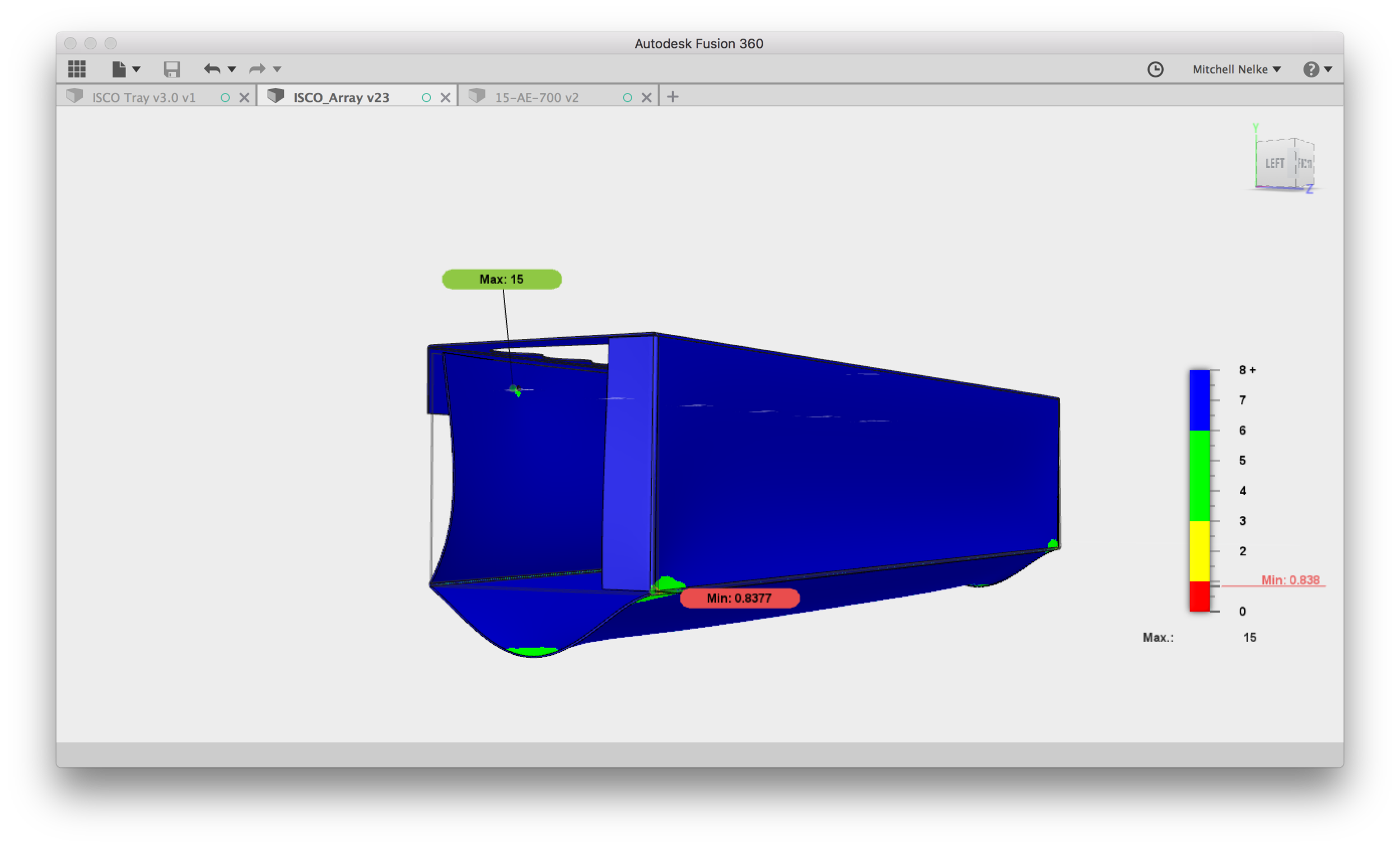
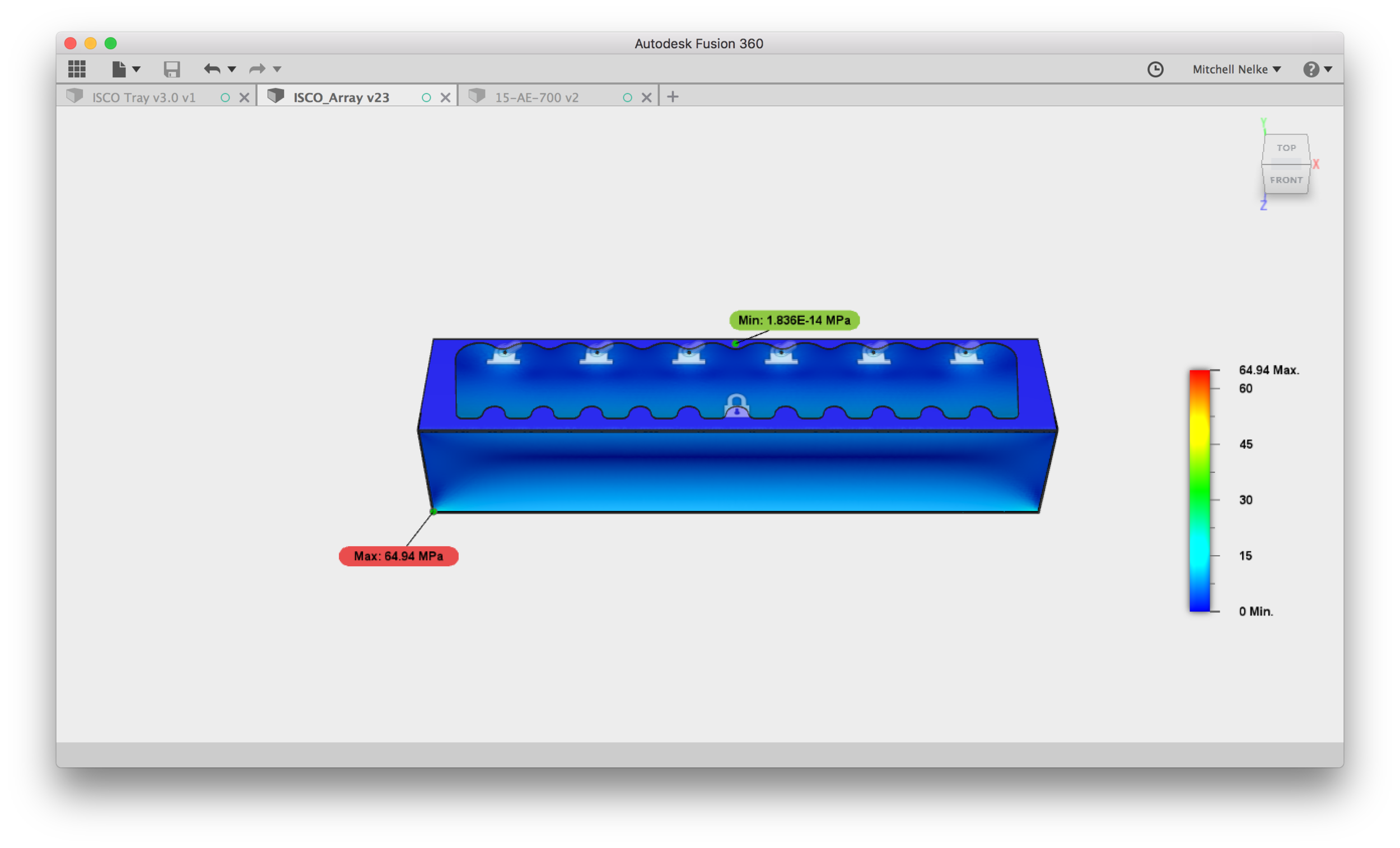
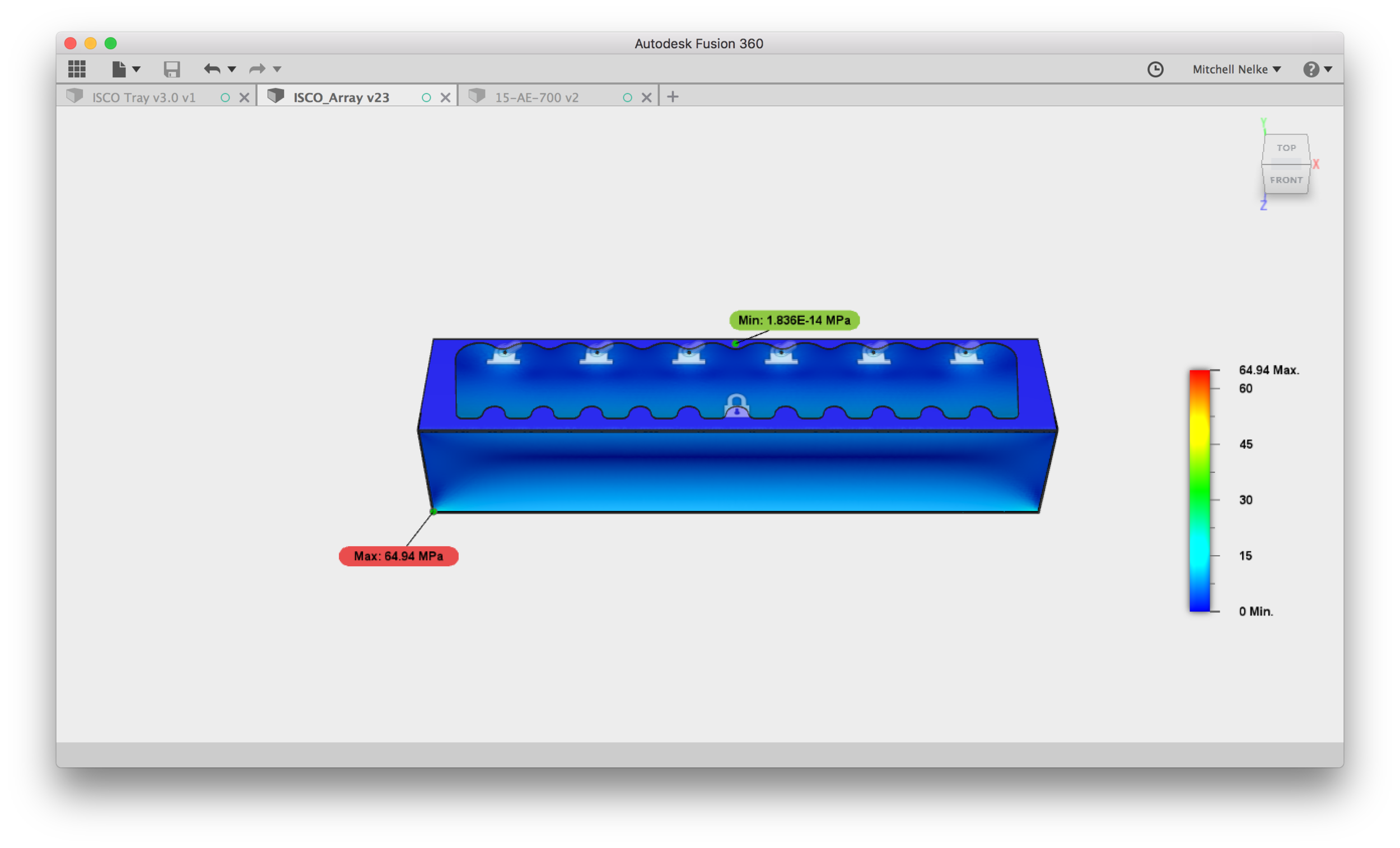
Safety factor is the ratio of applied stress over acceptable stress. A SF of 1 or lower means that under static conditions, the component will start to exhibit failure. This will improve greatly by the addition of glue in between the bolted flanges in addition to adding kevlar straps. However, if the tray was accidentally carried from the top face it would potentially break.
Iteration:
To account for additional stresses and accidental carrying methods, I decided to add an additional flange on the bottom that is the same length as the side flange, as shown below.
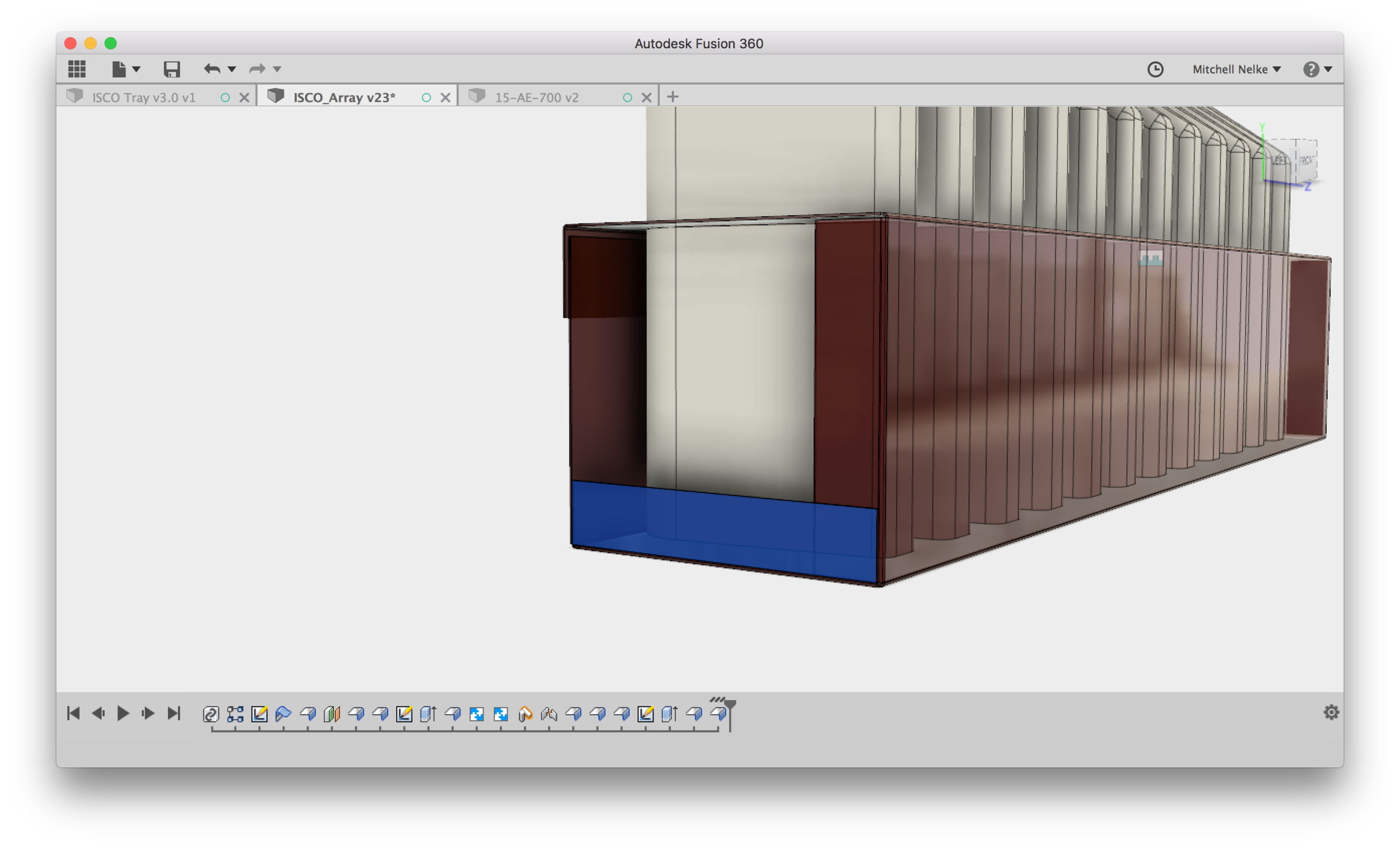
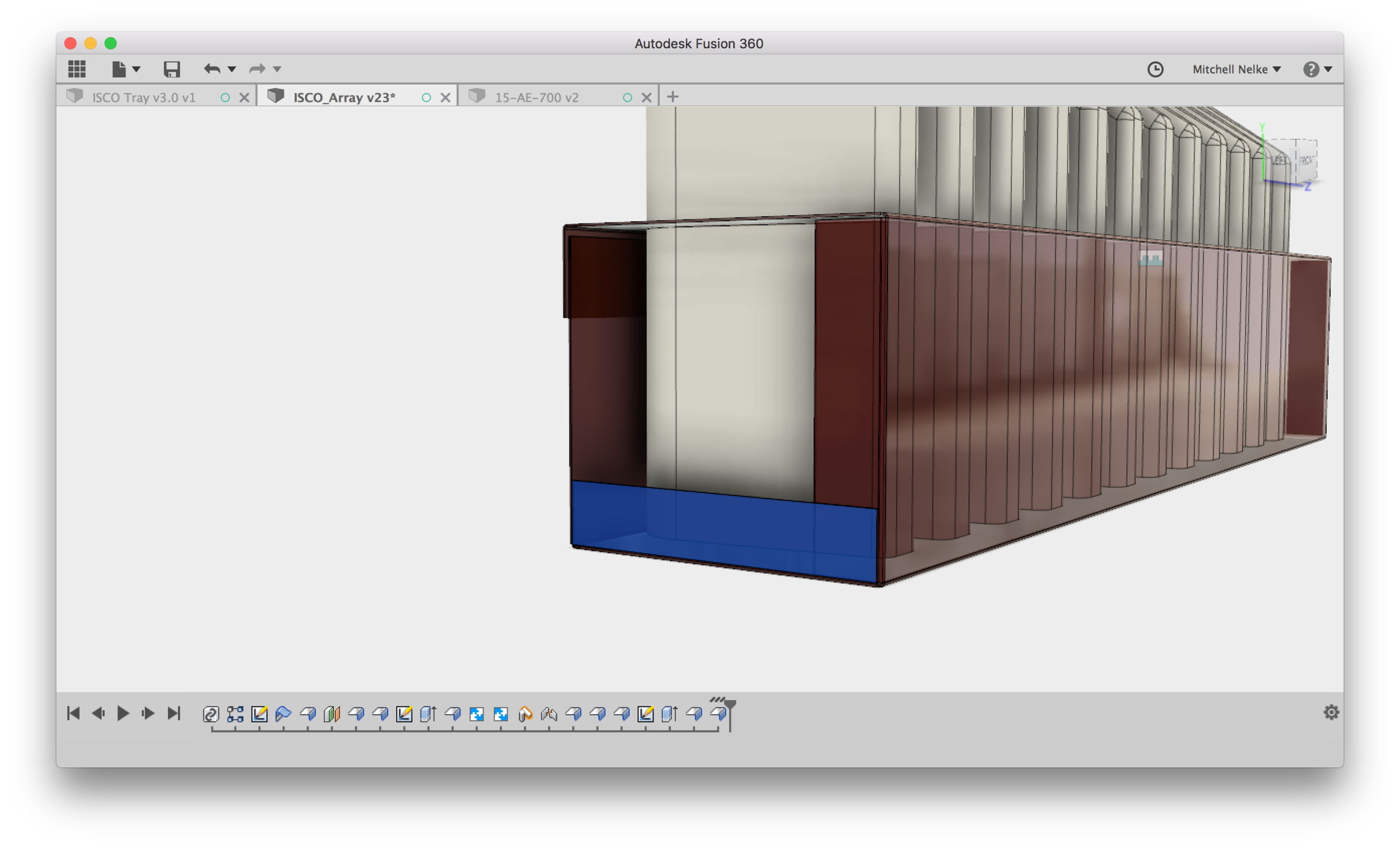
The results of the new simulation are much more promising:
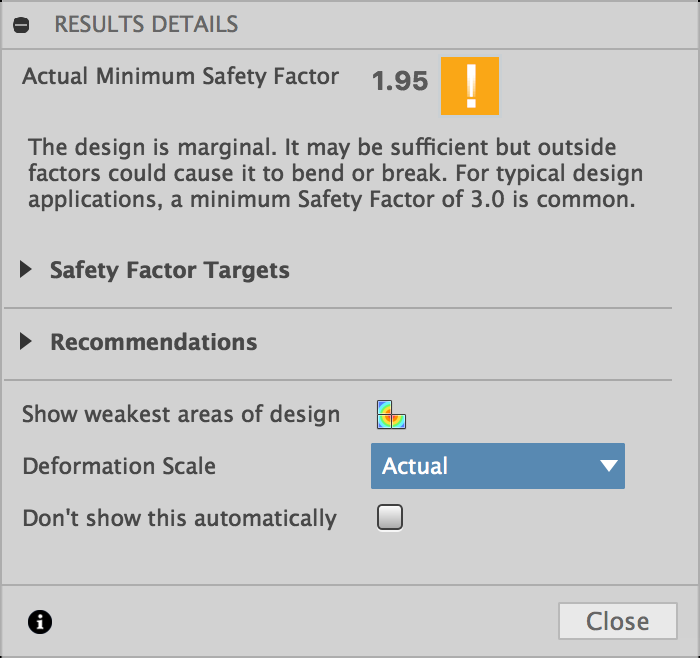
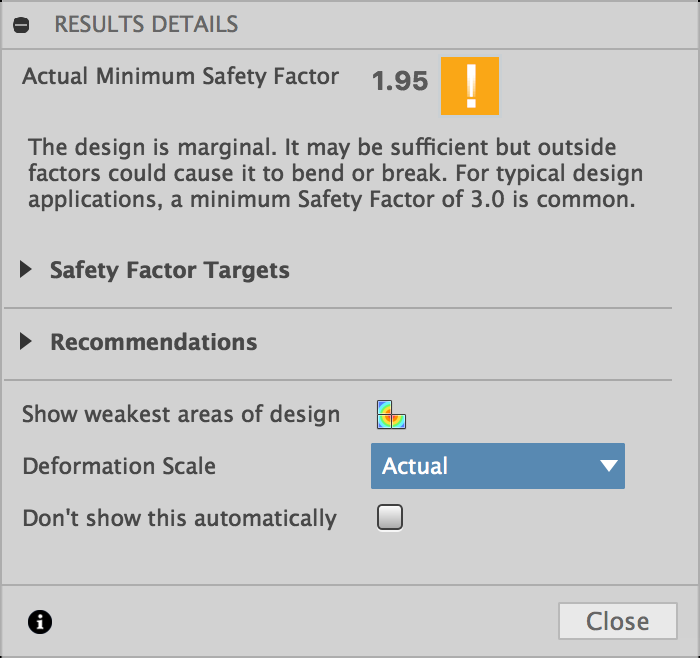
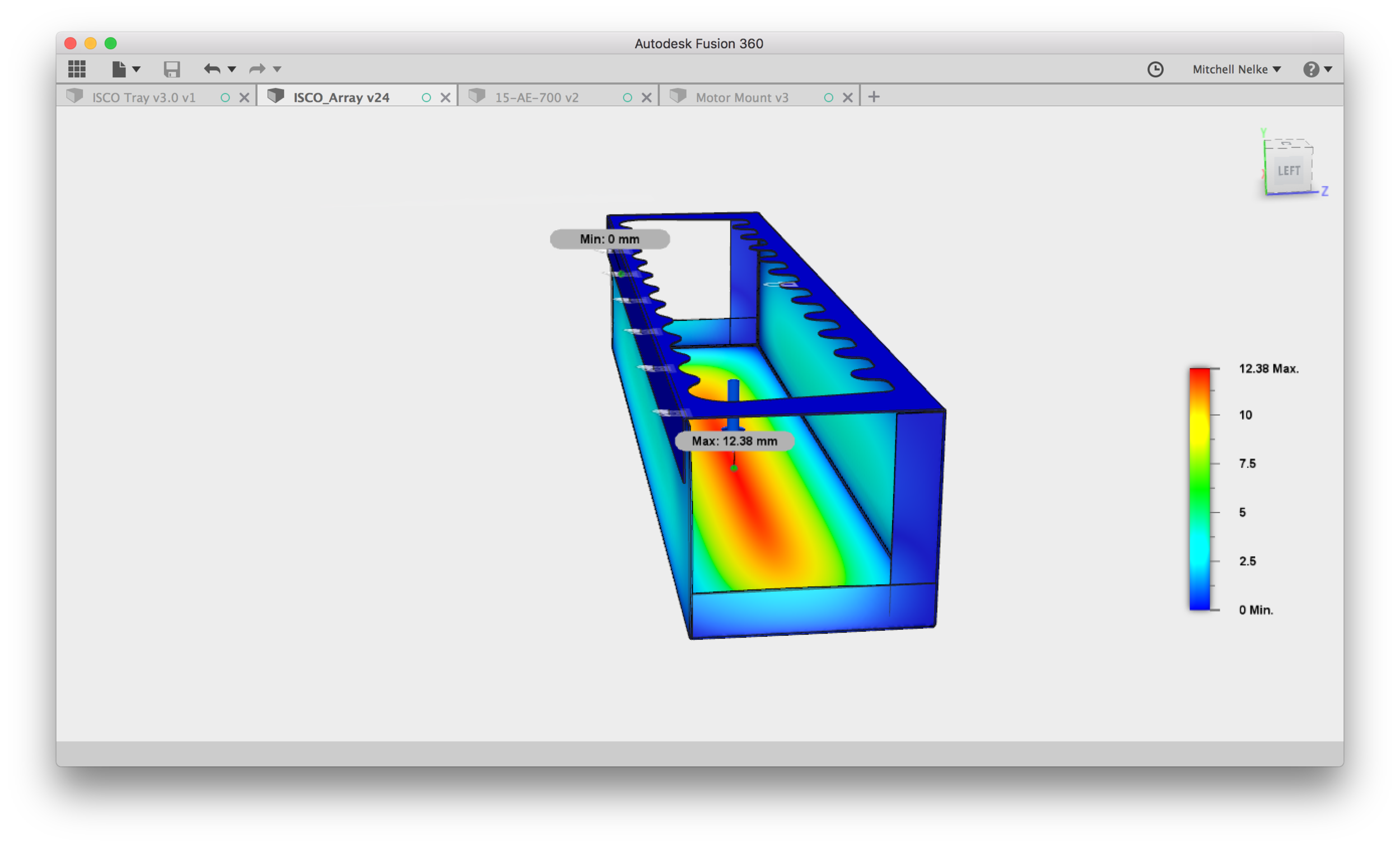
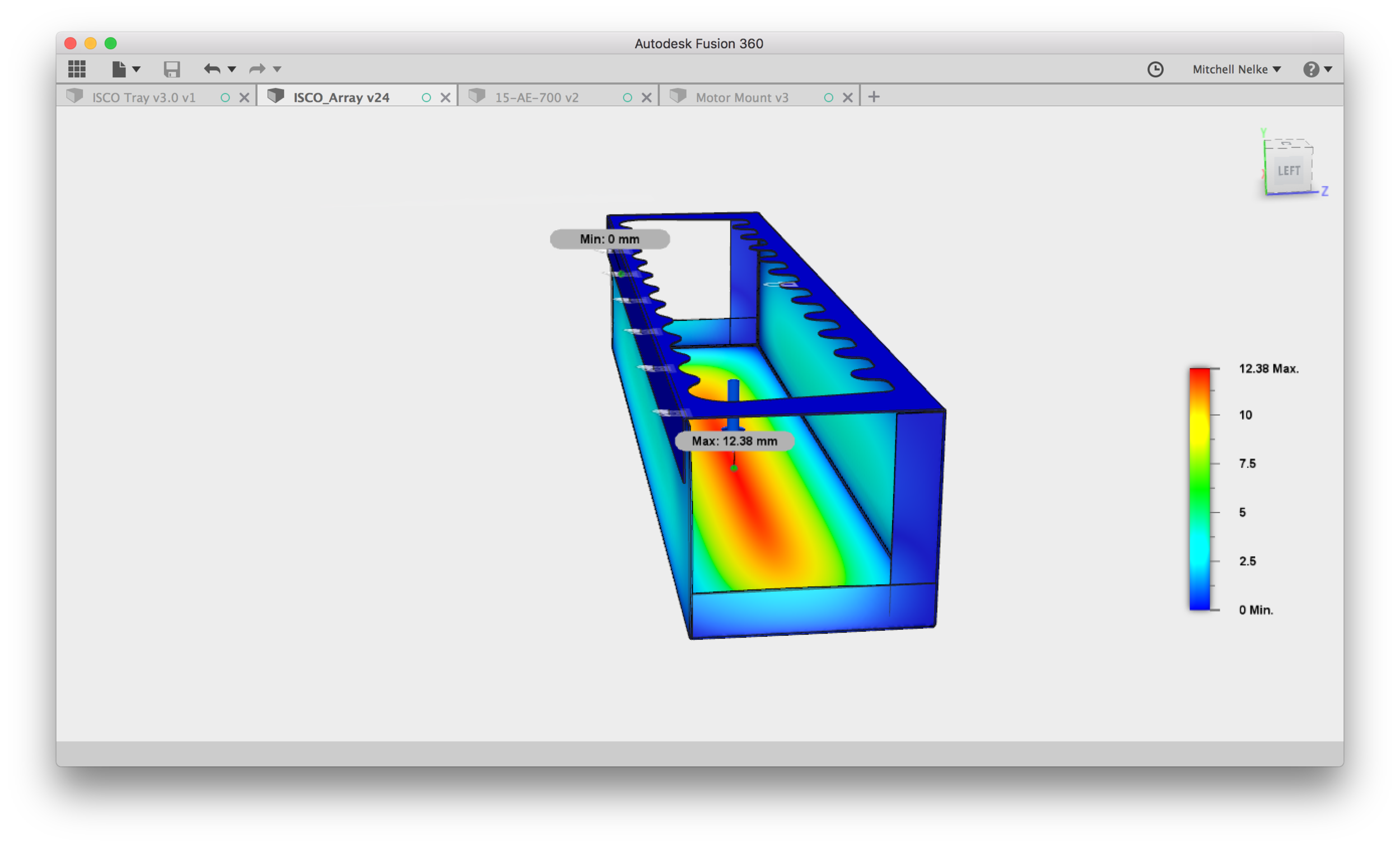
With the new flanges, the maximum deflection is slightly reduced and the safety factor is well above what is necessary. Because straps will be used rather than holding the tray from the top, the actual safety factor is likely much higher, but the tray is unlikely to break if accidentally picked up by the plastic.
Conclusion:
The new bottle tray was simulated with promising results. Larger safety factors and smaller displacements show that it is less likely to break under greater load, and the addition of straps to support the weight from the bottom will reduce the stress in the sheet plastic and provide the user with a more optimal carrying method.