The foam finally arrived and we have started to experiment with it. I cut various small 10 x 10 mm squares at different power levels, speeds and heights to determine our best settings. The settings that I observed were cutting the best: Power 17, Speed 23 and Height 3315.9mm.
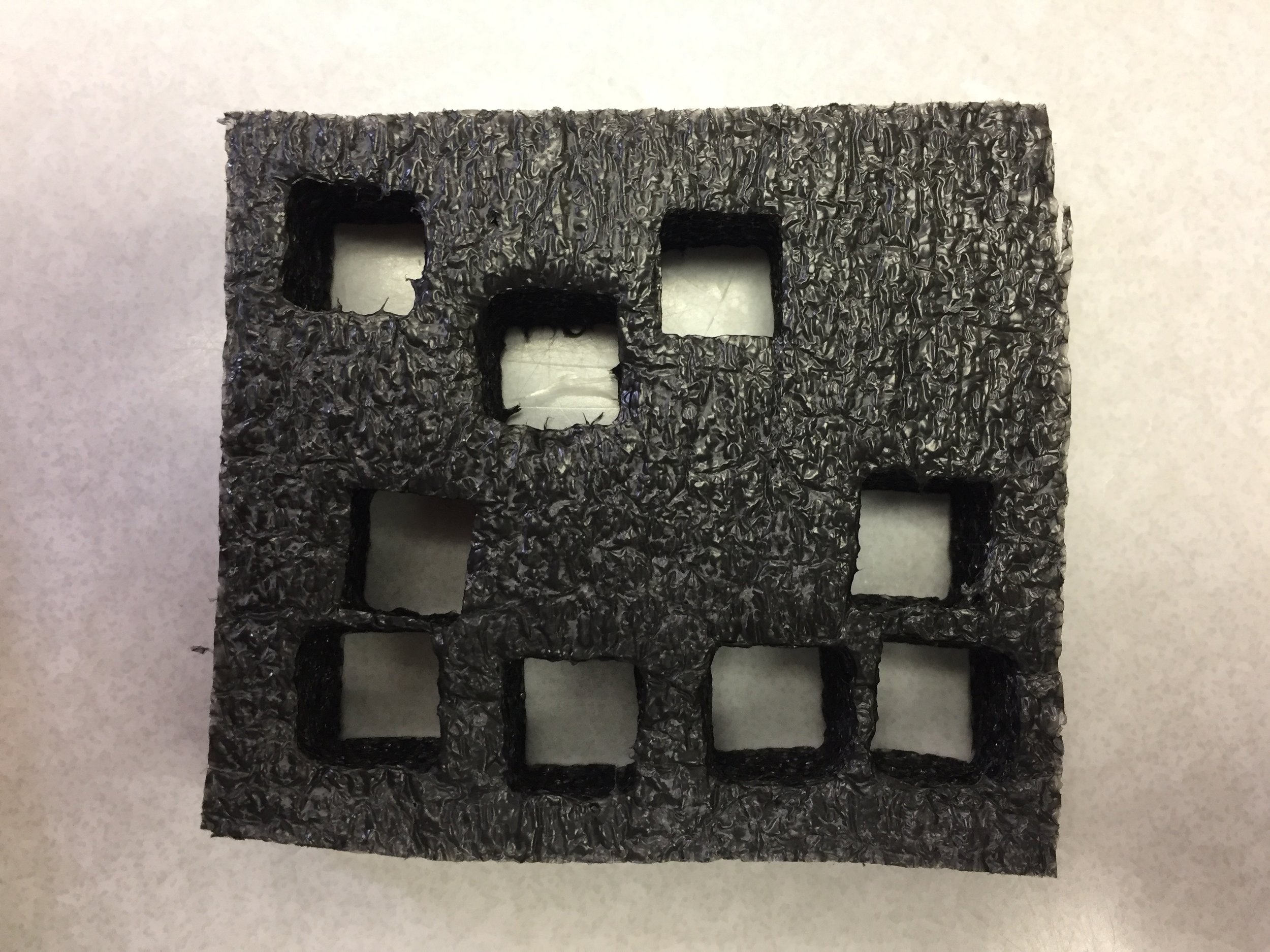
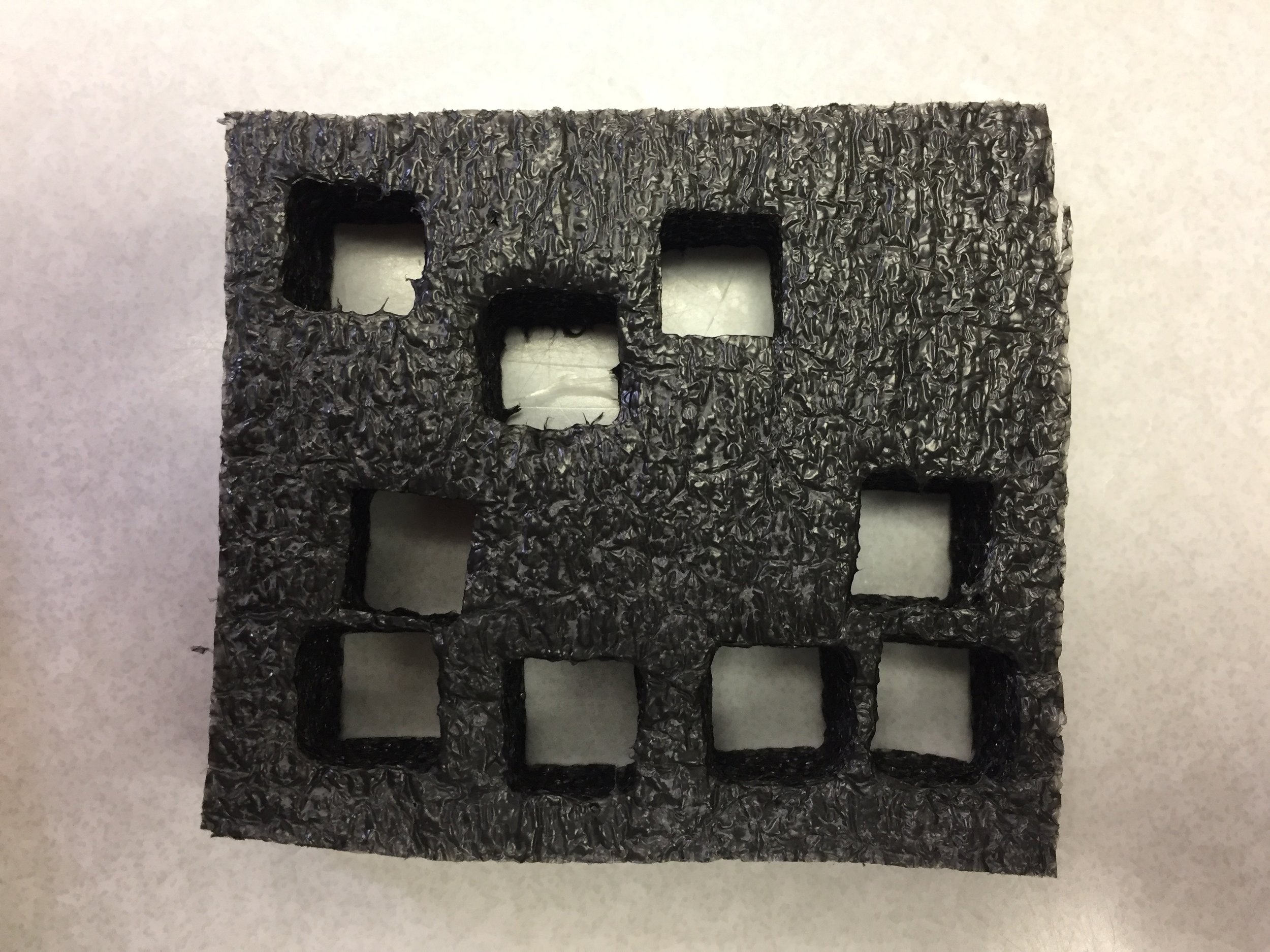
Sample cuts on foam
After doing some testing I intended to cut the foam inserts for the drawers. When loading the DXF file from Fusion360 on to MetalCut, the file appeared to be changed. There were some extra lines that were not supposed to be there. After analyzing the MetalCut file, I noticed that the program was making some discontinuities in the design outlines and created lines towards the center to compensate for it. I believe it was doing this because the file had some sharp edges and I think it doesn’t precess these edges very well.
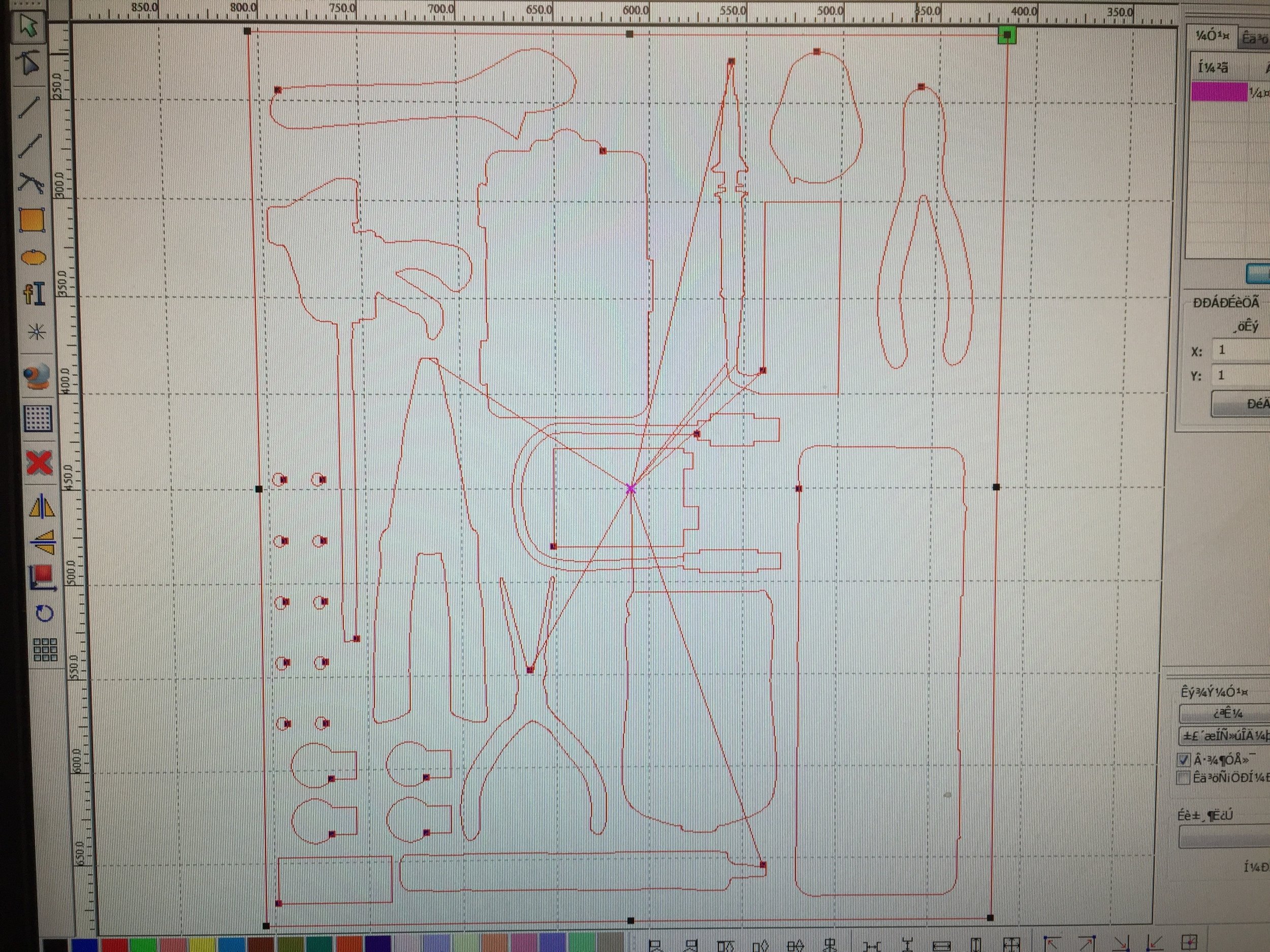
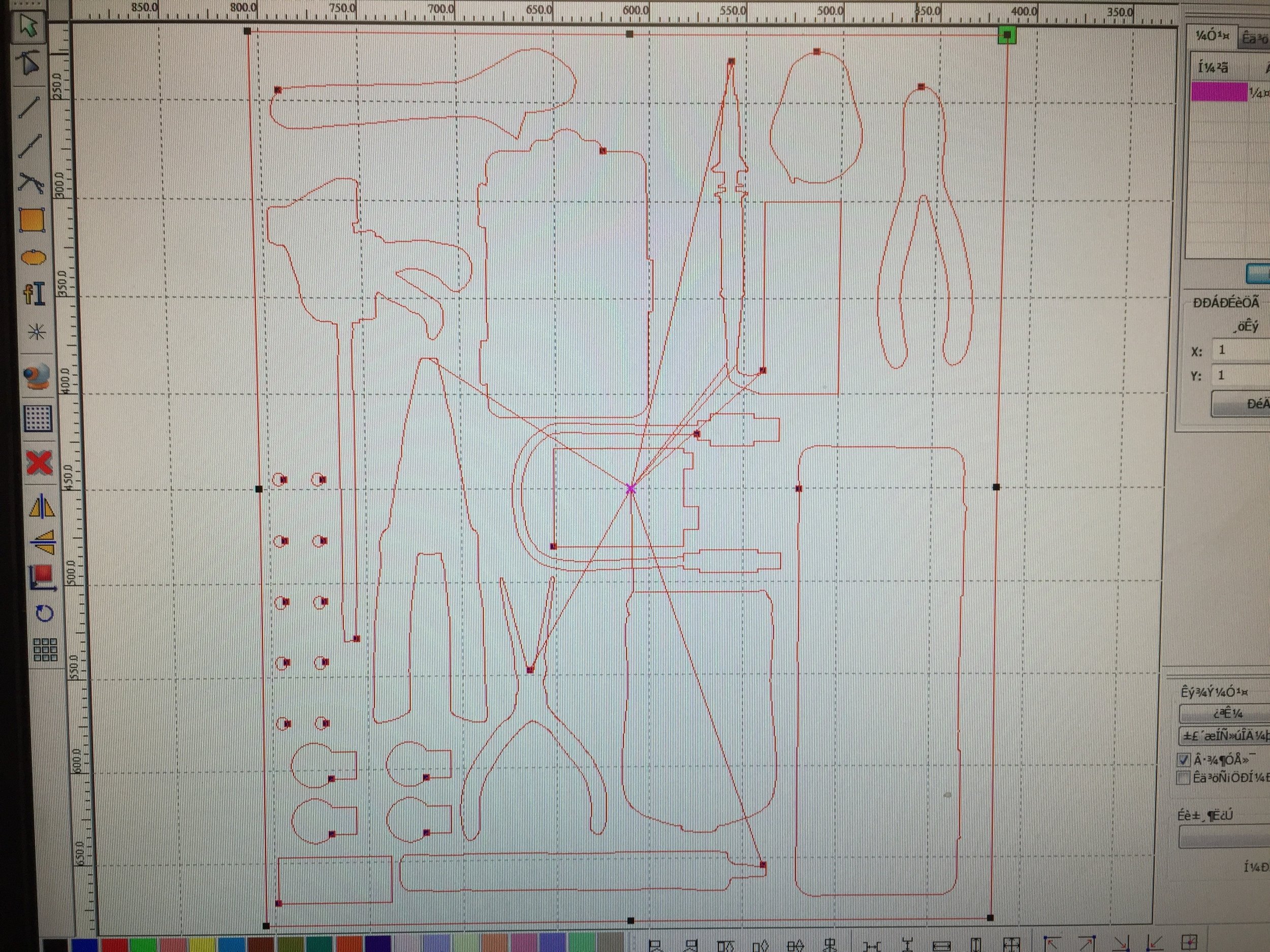
The Fusion360 design is being fixed. Only some pieces seemed to be affected by these sharp edges. After all the changes have been made, the cutting process should go smoothly.