Several design decisions were made based on our pump parameters needed. For example, we need at least one meter of pump head and we need to be able to move water through roughly 5 meters of 3/16” (.476 cm) tubing (most likely there will be less tubing involved, but this is a good number to start with).
Through observation, I found that the throughput of a single pump at 1m head and room temperature was 50mL/min, or .83 cm^3/s, and the maximum suction head is greater than 1.5 meters, which was the highest I could place the pump without creating a more complex setup.
With a tubing cross sectional area of .71 cm^2, the velocity of the water in the tube being moved by the pump is about 1.2 cm / s. With such a small velocity, the head loss directly resulting from the 26 tee joints is about .76 cm, and the head loss from the friction of the tubing is even less than that.
Because we don’t have to worry about head loss, and the max head one pump can provide exceeds our requirements, I decided that the design should combine two pumps in parallel to improve throughput rather than in series to improve head.
Now I could design the dual pump mount! I went with a design that mounted on the inside of the C-Channel spine, with the colinear, top-to-top facing pumps sticking out perpendicular to the c channel. The first 3D Print should be finished tomorrow! Pictures below.
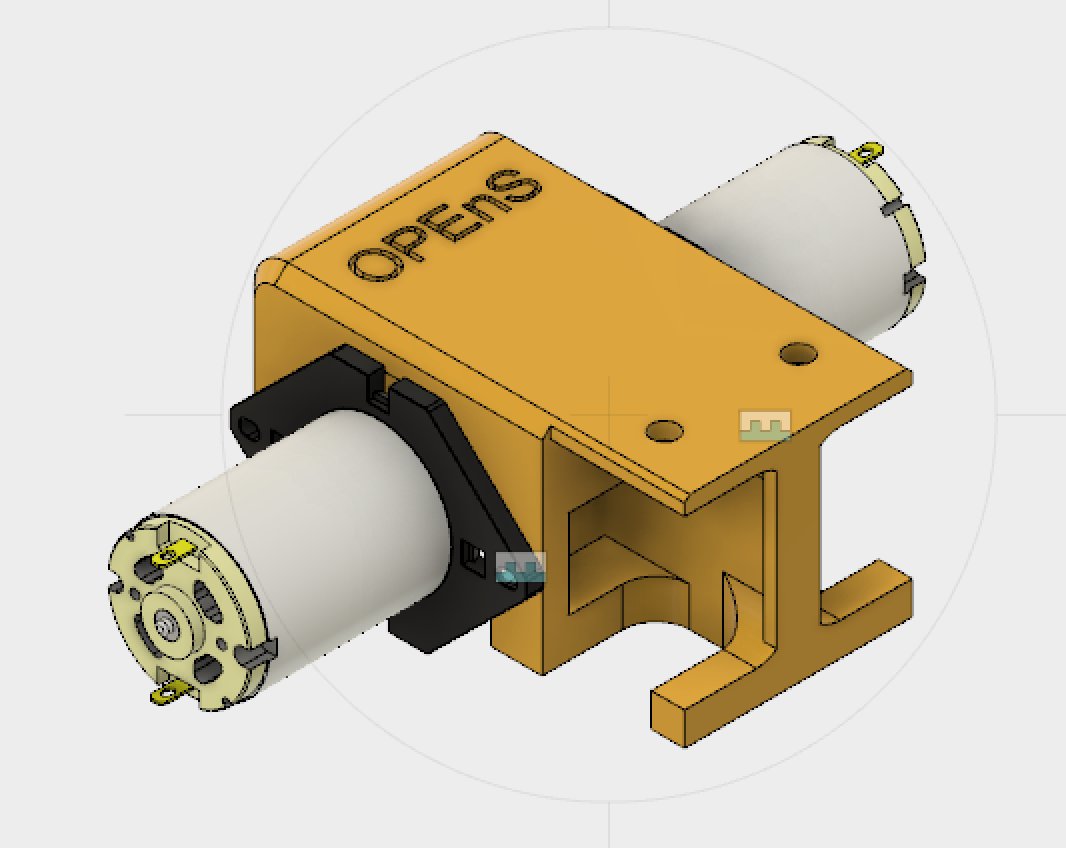
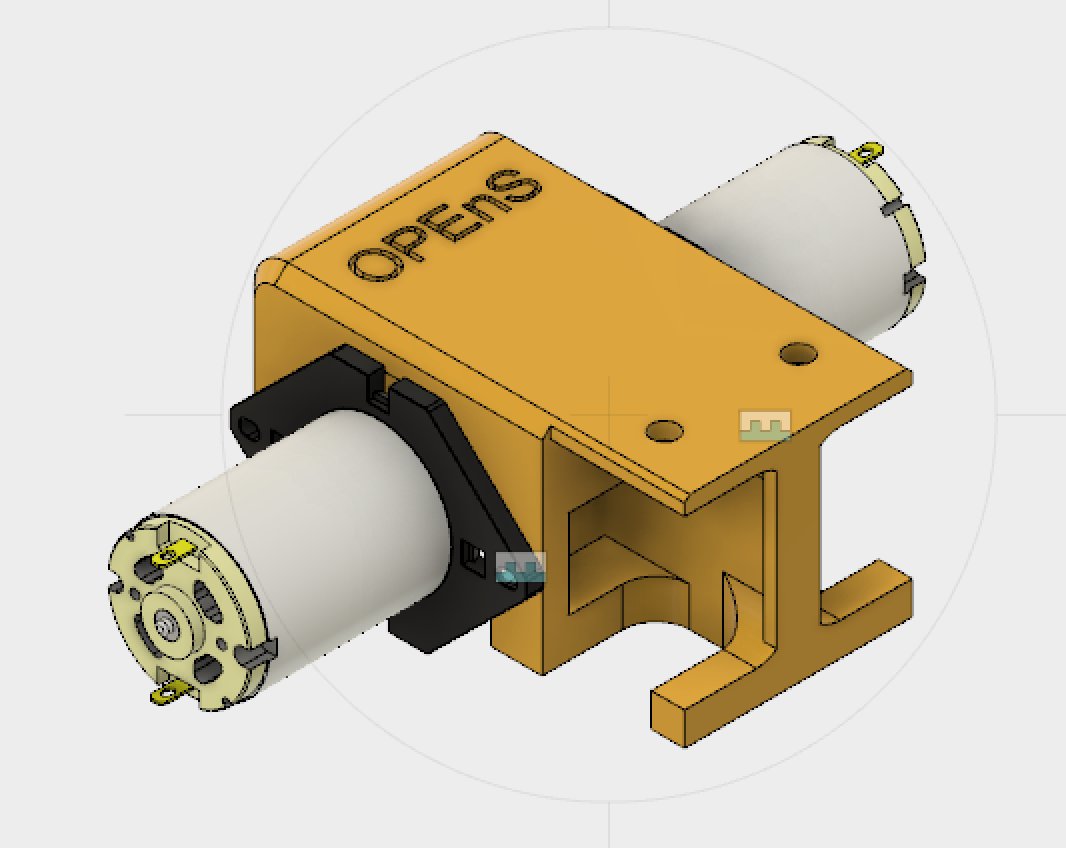